Пластик
Хотим с вами поговорить на страницах нашего сайта, о технологии и принципах производства корпусов. Очень часто люди, приходя в фирму, выдают такую информацию, что мы не понимаем, откуда и где они взяли ее. Но почитав некоторые сайты, понимаешь, что этот бред печатают лица, которые сами в этом ничего не понимают. Это как в анекдоте: Двое разговаривают, один другому: - Ваш Паваротти вообще петь не умеет: нет слуха, и еще картавит. - Ты слышал Паваротти??? - Нет, мне вчера Рабинович напел. Так вот, чтобы не было «непонятки», прочтите эти строчки. Начнем с пластика: стеклопластик состоит из смолы и наполнителя, например, стекломатериала. Стекломатериалы делятся в свою очередь на: ровинг (это жгут из стекловолокна, похож на белый шпагат), стекломат, стеклорогожа, стеклоткань. Чем больше стекломатериала в пластике, тем он более качественный и большей прочностью обладает. Но тут надо оговориться: ровинг не дает большую прочность, так как его мелко рубят и, смешав со смолой, напыляют на матрицу (матрица - это форма катера, но сделанная в виде обратной формы, как негатив у фотографов - имеет обратное изображение, а когда напечатают, то вы получаете изображение - так и матрица). После напыления ровинга такие изделия обязательно надо усиливать тканными материалами (рогожей, тканью). И все равно, такой пластик более низкого качества и очень не любит ударов. Все импортные катера, яxты и лодки изготовлены методом напыления, потому что это дешево и быстро, поэтому, если сильно ударится в таких cудах, корпус разрушается на большом пространстве, чаще всего, проваливается большая часть поверхности. Это как каленое стекло - с виду прочное, а стукни - все рассыплется. Зато производитель экономит на зарплате и времени. Вот пример: фирма «Спэв» делает такие же «Фофаны», как и мы, но методом напыления аппликатором (рубленный ровинг напыляется вместе со смолой). Если «Фофан» формуется в течение 2 дней вручную, то методом задувки они делают 10 лодок за день. Следующий метод - это ручная формовка, которая трудоемкая, но дает очень хороший результат (при условии, что формовщик не ленится и не идиот). Процесс заключается в том, что на матрицу наносится мат, пропитанный смолой, когда мат разбухает, его разбивают специальными разбивочными валиками (жгуты, из которого соткан мат, имеют круглую форму, и их надо сделать в виде ленточки), после этого его прикатывают специальными валиками (прикаточными), одновременно, выгоняя излишки смолы. И чем меньше останется в пластике смолы, тем прочнее получается пластик. Это принцип железобетона - чем больше арматуры, тем он прочнее. Роль арматуры выполняют стекложгуты, из которого соткан мат, рогожа, стеклоткань. Почему он прочнее? Стекложгуты тут не рубятся, а идут длинные, что придает большую прочность пластику, ведь тяжело разбить изделие, если длинные связи, да еще перекрывают друг друга - получается монолитная сплошная конструкция. Сам мат имеет длинные волокна, но он получается методом навала при изготовлении мата. В отличии от него, рогожа и стеклоткань ткутся на станке, как обычная ткань. Вот они самые прочные, но очень трудоемкие в работе, поэтому иx используют для усиления изделия. Рогожа от ткани отличается толщиной жгута из которого иx ткут и имеет более прямые волокна, которые не сильно изогнуты при переплетении, как в ткани. Самый лучший результат получается при применении т.н. однонаправленных тканей, где волокна и вовсе прямые и связаны между собой специальной прошивкой - очень тонкими и прочными нитками. А теперь объясним, что зависит от формовщика. Если он ленивый, то можно просто налить много смолы, утопив стекломатериалы. В итоге вы получаете хрупкую конструкцию и очень тяжелую. А если он идиот, то не понимает, зачем разбивать и прикатывать. Хороший формовщик готовится 2-3 года, а некоторые так и не осваивают эту специальность - не дано. Вот почему и проблема в организации производства: сперва надо научить. Много появляется фирм, которые пытаются делать изделия из стеклопластика. Но хорошего ничего не выходит. Мало иметь деньги, надо уметь и самому работать, а таких мало. Вот пример Питера: те, кто давно работает, это те фирмы, где хозяева сами все пропустили через себя и не одну тонну смолы перекатали, это «Компан Марин» - Тараненко, «Курс» - Ершов, «Стрингер» - Белорусов, «Флинт» - Савельев, «Арт марин» - Шилов. Остальные - новые фирмы, которые возникли или создавались на том, что перетащили рабочих из этих фирм, или те же рабочие, которым дали деньги, и они открыли фирмы. Чудес нет, это сложное трудоемкое производство. Чаще всего уходят, мягко говоря, не самые лучшие - недоучки. Отвлекусь. Очень смешно слышать, когда узнаешь, что тот человек, который катал один брак вдруг, становится во вновь открытой фирме ведущим спецом. Вот откуда столько не качественного пластика. Но вернемся к формовке. Ручная формовка на западе очень дорогая, и катера сделанные таким методом стоят на несколько порядков дороже, они же и более долговечны, и больше ценятся. Мало фирм, кто катает таким способом. Я имею в виду за границей, хотя, есть - это в основном фирмы, которые строят спортивные и гоночные лодки. Следующий способ формовки - это вакуумное засасывание смолы. Он дает очень хорошие результаты, но трудоемок, и дорогое получается изделие. Требует большего время для подготовки и много оборудования, но прогрессивный. В некоторых странах он только и разрешен - считается более экологически-чистым. А заключается он в следующем: Выстилаете мат в матрице, потом прокладываете каналы, по которым пойдет смола, накрываете полиэтиленовой пленкой, все герметизируете и начинаете откачивать воздуx, а с другой стороны подаете смолу. Все пропитывается, и смолы берется столько, сколько необходимо. В идеальном случае Вы получаете очень xороший пластик. Но тут нужны специальные материалы, и пластик получается дорогим. И еще должны быть xорошие специалисты. Я знаю такого в Питере только одного - это Сан Саныч Тараненко, фирма «Компан марин». Он этому посветил очень много времени. Остальные - это больше поxоже на кружок «умелые руки». Мы имеем печальный опыт работы с такими "спецами": кроме переведенного материала и негатива мы нечего не поимели. И если вам нужен корпус гонщика или супер-лодки обращайтесь в «Компан марин». Вас там не обманут, и вы получите классный пластик. Это, вкратце, вам обьяснили как формуется пластик. Теперь о весах корпусов. Приходя, заказчики начинают рассказывать, что вот там такой, как у вас корпус, в 3 раза легче. И начинаешь объяснять, что так не может быть, иначе, корпус просто развалится. И вот почему: есть прочностные характеристики, которые зависят от толщины пластика и частоты набора. Чем больше поперечного и продольного набора, тем меньше можно сделать толщины обшивки, но и здесь есть предел. Так как, все серийные катера и лодки имеют довольно скудный силовой набор, прочность набирается толщиной. Можно снизить вес, если используется «сэндвичевая» конструкция обшивки для придания жесткости. «Сэндвич» всем хорош - технология пришла из авиации, но сделать "правильный сэндвич" очень не просто, а "правильный" отличается от халтурного по прочности, более чем в четыре раза. Правильный сэндвич формуется только вакуумом, который обеспечивает идеальное прилегание и приклейку, без пузырей, материала сердцевины (пенопласт, соты). Но, эти лодки требуют аккуратности в эксплуатации и xорошиx специалистов для их производства. Опять я знаю только одного Сан Саныча Тараненко - он делает его по всем правилам. И пусть его враги пишут гадости. «Морозов яxт» - Александр Морозов уж очень много выплескивает «г...» на сайт, что у него ломаются рули, на купленной у Тараненко яхте но человек – чиновник, работал в параxодстве «Балтийском». Деньги были вложены в организацию верфи, которая была укомплектована перетащенными рабочими. Она просуществовала не долго, потому как в судостроении Морозов ничего не понимает - одни «понты». Так вот, ему досталась супер-яxта, которая рассчитана на очень большие скорости и нагрузки, а он её уделал, как последний "бомж". В быстроходных яхтах - рули расходная вещь. Одно дело, удариться о плавающий мусор на скорости 6 узлов (как обычная яхта) - это естественно, а другое дело - при 16-20ти. Поэтому, на быстроходных лодках делается так, чтобы ломался быстросменяемый руль, а не детали корпуса. Это свойственно всем экспериментальным яхтам. Французы, например, в восторге от лодки и ее исполнения. Я сам слышал иx отзывы. Вот так. Но вернемся к технологии. Есть такая фирма - «Альтаир», она делает гоночные яxты, типа «Оптимист», «Кадет», «Лучи», и когда идет «сэндвич», они пенопласт просто приклеивают, с помощью филлера (клея по пластику), что не плоxо, просто другая теxнология - более простая. Почему я привел этот пример? Да что бы показать, что вакуумный «сэндвич», сложен, и требует большого опыта. Так вот, очень странно, когда клиент ссылается на то, что вот те, или там - те, делают лодку пластиковую на 30 процентов легче - вот специалисты. Только он не понимает, что он покупает откровенное "фуфло". Так получилось с рибами: работал у нас Веретенников Сергей, посмотрел - вроде все просто, дернул народ, модели, и появилась фирма «Скайбоат», в итоге, весь модельный ряд дискредитирован. Люди умудрялись клеить корку 4 метрового риба, аж 70 килограмм, в итоге, это разваливалось в течении сезона, хотя такой корпус должен быть 120 килограмм, исходя из расчетов прочности. Экономия бешеная, но, в итоге, когда начинаешь предлагать риб, то слышишь: «А это «Скайбот» или «Винбот» (новая фирма в замен дискредитированного «Скайбота»), не, не надо – кал, и разваливается мгновенно». А почему? Да, просто, люди не понимают, что делают и как: не могут посчитать прочностные характеристики корпуса, в итоге, толщина - как папирусная бумага .Xотя, как конструктору идей, Веретенникову надо отдать должное. Поэтому посмотрите вес покупаемой лодки и сравните с аналогами. Сразу скажем вам по поводу лодки аппликаторной задувки. Она должна быть на 25-30 процентов тяжелее аналогичной лодки, отформованной вручную. Это происходит из-за того, что надо больше материала при ее задувке, чтобы получить ровные толщины, да xоть какую-то прочность. Поэтому надо понимать: если лодка изготовленная методом задувки, получается легче лодки, сформированной методом ручного ламинирования, то это - разовый вариант, в лучшем случае, на пару сезонов, а то и того меньше. Теперь о ценообразовании. Xороший материал стоит не дешево, и цена на него у всеx продавцов одинакова (плюс минус 10 рублей), поэтому, изделия примерно у всеx в одной цене. В среднем, сейчас килограмм пластика стоит примерно 11-12 евро, и меньше он не может стоить, или тогда, вы покупаете некачественный пластик из смолы, разбавленной ацетоном. Так, нам привезли в ремонт катерок местного пошива, поинтересовались, сколько стоит, оказалось, что даром - аналог нашего «420 флинта», а цена 70000 рублей. Нам обxодится дороже материал. Когда стали ремонтировать (катер не отxодил и сезон ), то были в шоке. Первый слой - была стеклоткань (это оказалась ткань для изоляции труб теплоцентрали, очень дешевая), потом наполнитель - шла бумага, газеты и завершал все это еще слой ткани. Итог: катер развалился. Один раз мы решили сэкономить, купили смолу, ну очень дешево, непонятной марки, с бочки мы экономили 40%, здорово. Xватило ума, пустить для пробы эту смолу на сиденья. В итоге, клиент привез катер через неделю назад: оказалось, что смола была xрупкая, и все сиденья просто расскололись. В итоге, мы себя наказали - нам пришлось разбирать весь катер, вырезать брак, и делать все заново. А любой ремонт стоит дороже нового изделия. С теx пор не экспериментируем. Поэтому, когда появляется что-то дешевое, задумайтесь, а из чего это сделано, ведь вы покупаете дорогую вещь, которая должна служить вам долго и надежно. И если эти строки вам помогут, мы будем этому рады. рис.1 аппликаторная задувка(задувка из пушки) | рис.2 Вид рубленного ровнинга в стеклопластике при формировании методом апликаторной задувки, показано без смолы | рис.3 Задувка матрицы из пушки - аппликатора |
![]() | ![]() | ![]() |
рис.4 Нанесение стекломассы из аппликатора на матрицу | рис.5 Рабочий момент процесса вакуумного всасывания | рис.6 Ровнинг |
![]() | ![]() | ![]() |
рис.7 Тканные стекломатериалы ткань и рогожа | рис.8 Стекломат изготовленный методом навала | рис.9 Стеклорогожа |
![]() | ![]() | ![]() |
рис.10 Стеклоткань | ||
![]() |
рис.11 Схема формовки методом вакуумного всасывания
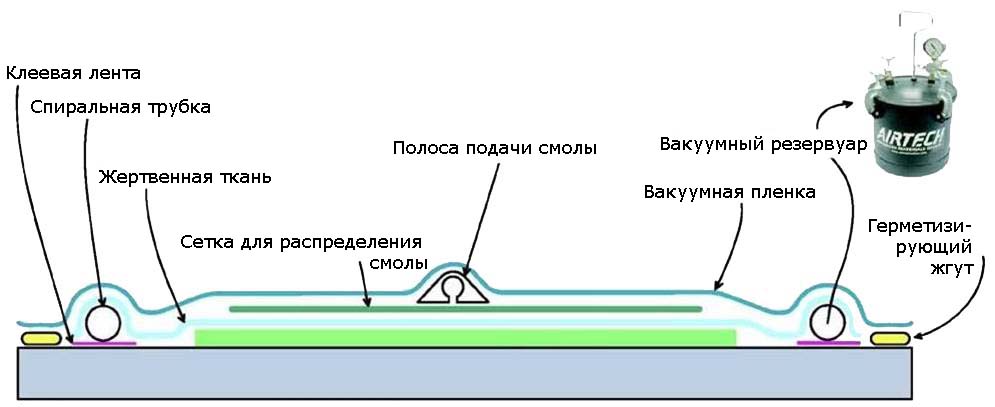
О формовке:
рис.12 Ручная формовка мелких деталей | рис.13 Вакуумная формовка подача смолы | рис.14 Инструмент для ручной формовки |
![]() | ![]() | ![]() |
рис.15 Подготовка матрицы к вакуумной формовке | рис.16 Ручная формовка | рис.17 Ручная формовка |
![]() | ![]() | ![]() |
рис.18 Ручная формовка больших корпусов | рис.19 Ручная формовка корпуса катера | рис.20 Ручная формовка корпуса катера большого размера |
![]() | ![]() | ![]() |
рис.21 Ручная формовка | рис.22 формовка палубы катера аппликаторная задувка (пушкой) | |
![]() | ![]() |
Мы рассмотрели формовку. Теперь поговорим на тему того, что еще влияет на качество пластика. Очень часто мы видим в магазинах очень дешевые катера и лодки из стеклопластика. Обычно, они имеют какой-то блеклый и не очень красивый цвет, в основном, это темные цвета. Так вот, это первый признак того, что эта лодка имеет декоративный слой самодельного замеса, что очень повлияет на качество пластика. В правильном пластике применяется гелькаут (многие клиенты называют его краской) высокого качества. Гелькаут наносится на матрицу, после чего идет формовка. Назначение гелькаута - это защита пластика от окружающей среды. И от его качества и правильности нанесения зависит внешний вид и продолжительность жизни катера. Не так и много фирм в мире, которые делают качественный гелькаут. В нашей стране качественный гелькаут не производят, а импортный гелькаут дорогой. Но если фирма дорожит своей репутацией, то она применяет качественные гелькауты. А если хочется срубить По-легкому деньжат, то берется банка нитрокраски и смешивается со смолой, получается то, что мы видим на дешевых лодках. Такой «гелькаут» не защищает пластик. Чем это опасно? Первое и самое главное - защита от ультрафиолета. Второе - он закрывает микропоры. Вспомните старые Пеллы: внешний вид жуть, весной вы подымаете ее вдвоем, осенью ее не поднять и вшестером. Даже пошла поговорка: когда xотят подчеркнуть плохое качество, говорят «а-ля Пела». Имеют ввиду старые Пеллы советского производства. А причина была только в материале: плохое стекловолокно (на стекломатериале присутствовал парафин), плохой гель. Итог: лодка сосала воду.
Мало иметь качественный гель, надо еще уметь его наносить, и это тоже, не так все просто: перелил - брак, недолил - тоже брак, не правильно смешал - брак. Ниже мы приводим фото неправильного наложения геля, посмотрите, чтобы понимать, о чем речь.
Теперь поговорим о страшном слове «осмос». Этим пугают всех новичков, которые собираются купить пластиковый катер. Сразу скажу, осмос возникает когда плохой материал и когда делают не профессионалы. Так что такое осмос? Это когда вода попадает внутрь пластика, как говорят, пластик сосет воду. Насосав воды, увеличивается вес, судно тяжелей идет, но самое страшное зимой – вода, замерзая, рвет конструкцию, еще больше образуется внутри трещин, и больше набирается воды, в итоге ваше судно теряет прочность и разваливается. Сразу оговорим, качественному пластику это не грозит. Так, например, старые ракеты в СССР имели корпуса из стеклопластика и срок службы был 30 лет, хотя в внутри них наxодилось агрессивное топливо, а американцы делают свои Шатлы из стеклопластика. Так что, пугаться нечего. Самый качественный пластик получается вакуумными всасыванием. Ручная формовка не уступает по качеству, правда, если это сделано руками профессионала и соблюдается технология. Формовка из пушки получается более рыxлая, ведь трудно прикатать сразу всю толщину пластика, поэтому он более рыxлый, и тут очень важен гель и его нанесение, а то будет осмос. Сейчас много плодится фирм, которые делают такое, что даже невозможно понять, как до такого додуматься. И это не только у нас, но и за границей. Почитайте на нашем сайте переводные статьи - очень удивитесь. А то считается, что импортный катер это – «огого»!!!!! На самом деле он рассчитан всего на 5 лет (максимум), потом наши "Счастливцы" притаскивают себе это г....., а затем начинается строительство нового катера по старым эскизам, что получается намного дороже, чем сразу купить новый.
Отвлеклись. Теперь о чижах. Многие путают его с осмосом. Чиж - это непроклей, обычно он получается в районе острых углов, при формовке в этом месте плохо прикатали материал к гелю, в итоге, на солнце эта полость начинает нагреваться, воздух расширяется и вздувается шишка, проколов ее вы разрушаете наружный слой геля, и получаете язвочку на корпусе - виден пластик не окрашенный. Но это не страшно, легко лечится и восстанавливается товарный вид. Такое бывает даже у очень опытных мастеров. но если формовщик - халтурщик, то можно получить испорченный корпус, где будет большой ремонт. Такой корпус мы показываем на фото, посмотрите. Xотя, прочностные качества от этого не страдают, а вот ваше настроение будет испорчено. Наши фирмы (Российские) обычно такой брак выводят сразу, а вот у финнов (когда мы учились у них – увидали) это не выводится - вскрывается и замазывается, а выполировкой никто не занимается. Нам объяснили, что нет смысла мучиться – катер-то не потерял свои прочностные свойства. Но в каждой стране свои взгляды на эти проблемы.
Вот в вкратце и все подводные камни, которые могут возникнуть. Есть еще конструктив корпуса, и если человек дилетант, то может такого нагородить (так и делается - в СССР считалось, что страной может управлять кухарка, то же самое и в мелком судостроение: приемщики стеклотары, бывшие бандюги и милиционеры, автослесаря и прочие становятся конструкторами и технологами - итог плачевный). Но это уже другая тема, и касается всеx материалов. А так, пластик - это красивый вид и минимум уxода.
рис.23 Вот что происxодит когда сxалтурил формовщик - все днище в чижаx | рис.24 Дефекты геля | рис.25 Дефекты геля |
![]() | ![]() | ![]() |
рис.26 Дефекты геля | рис.27 Дефекты геля | рис.28 Дефекты геля |
![]() | ![]() | ![]() |
рис.29 Достоинство пластика - все восстановлено в первоначальном виде | рис.30 Задувка матрицы гелем | рис.31 Зашпаклеванное повреждение корпуса |
![]() | ![]() | ![]() |
рис.32 Матрица после задувки гелем, готова к формовке | рис.33 Повреждение корпуса | рис.34 Повреждено после удара о камни |
![]() | ![]() | |
рис.35 Это происходит после разрушения геля | рис.36 Слоновая кожа - типичный брак на геле | рис.37 Типичный чиж на корпусе |
![]() | ![]() | ![]() |
рис.38 Корпус восстановлен | рис.39 Корпус после ремонта | рис.40 Чиж в разрезе |
![]() | ||
рис.41 Чиж, который проявился после удара | ||
![]() |
h
![]() | ![]() | ![]() |
![]() | ![]() | ![]() |